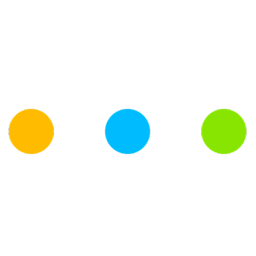
Ball and rod mills
Lời nói đầu
TCVN 4362 : 1986 do Viện luyện kim màu - Bộ Cơ khí và Luyện kim biên soạn, Tổng cục Tiêu chuẩn đo lường Chất lượng trình duyệt, Ủy ban Khoa học và Kỹ thuật Nhà nước (nay là Bộ Khoa học và Công nghệ) ban hành.
Tiêu chuẩn này được chuyển đổi năm 2008 từ Tiêu chuẩn Việt Nam cùng số hiệu thành Tiêu chuẩn Quốc gia theo quy định tại khoản 1 điều 69 của Luật Tiêu chuẩn và Quy chuẩn kỹ thuật và điểm a khoản 1 điều 6 Nghị định số 127/2007/NĐ-CP ngày 1/8/2007 của Chính phủ quy định chi tiết thi hành một số điều của Luật Tiêu chuẩn và Quy chuẩn kỹ thuật.
MÁY NGHIỀN BI VÀ NGHIỀN THANH
Ball and rod mills
Tiêu chuẩn này áp dụng cho các máy nghiền bi và nghiền thanh sử dụng trong ngành công nghiệp mỏ và các ngành công nghiệp khác để nghiền ướt các loại quặng và vật liệu.
Tiêu chuẩn này không áp dụng cho các máy nghiền bi có thân hình côn và các máy nghiền bi có tấm lưới ở cửa tháo liệu mà tỷ lệ giữa chiều dài và đường kính của thùng nghiền lớn hơn 1,5.
1. Kiểu, thông số và kích thước cơ bản
1.1. Máy nghiền phải được chế tạo theo các kiểu sau:
NBT: Máy nghiền bi, cấp và tháo liệu trung tâm, vật nghiền là bi cầu, có tấm lưới ở cửa tháo liệu; NB: Máy nghiền bi, cấp và tháo liệu trung tâm, vật nghiền là bi cầu;
NT: Máy nghiền thanh, cấp và tháo liệu trung tâm, vật nghiền là thanh hình trụ.
1.2. Những thông số và kích thước cơ bản phải theo chỉ dẫn trên Hình vẽ và các Bảng sau:
- Bảng 1: Máy nghiền bi có tấm lưới;
- Bảng 2: Máy nghiền bi và thanh nghiền không có tấm lưới.
Bảng 1
Tên thông số và kích thước cơ bản | Kiểu máy | ||||||||||
NBT 500 x 300 | NTB 900 x 900 | NBT 1200 x 1200 | NBT 1500 x 1600 | NBT 2100 x 2200 | NBT 2700 x 2700 | NBT 3200 x 3100 | NBT 3600 x 4000 | ||||
1 đường kính trong của thùng | 500 | 900 | 1200 | 1500 | 2100 | 2700 | 3200 | 3600 | |||
2 Chiều dài thùng, mm | 500 | 900 | 1200 | 1600 | 2200 | 2700 | 3100 | 4000 | |||
3 Dung tích danh nghĩa của thùng, M3 | 0,056 | 0,45 | 1,0 | 2,2 | 6,3 | 13,0 | 22 | 35,5 | |||
4 Kích thước choán chỗ của máy, không lớn hơn, mm | Dài L | 2100 | 3200 | 4200 | 5400 | 8100 | 8900 | 9700 | 13,800 | ||
Rộng E | 1300 | 2100 | 2700 | 3200 | 4800 | 6400 | 6400 | 7800 | |||
Cao H | 850 | 1100 | 1700 | 2800 | 3800 | 5100 | 5200 | 5700 | |||
5 Tần số quay danh nghĩa của thùng, tính bằng % của tần số quay tới hạn | 75 – 85 | ||||||||||
6 Công suất động cơ điện, không lớn hơn, kw | 4 | 15 | 30 | 55 | 160 | 315 | 630 | 1000 | |||
7 Khối lượng toàn bộ máy, (không kể bi); không lớn hơn, tấn | 1,050 | 3,6 | 8,1 | 13,5 | 43 | 71 | 97 | 160 | |||
8 Tổng khối lượng của bì, không lớn hơn, tấn | - | 1 | 2,2 | 4,8 | 15 | 31 | 52 | 82 | |||
Bảng 2
Tên thông số và kích thước cơ bản | Kiểu máy | |||||||
NT 900 x 1800 NB 900 x 1800 | NT 1200 x 2400 NB 1200 x 2400 | NT 1500 x 3000 NB 1500 x 3000 | NT 2100 x 3000 NB 2100 x 3000 | NT 2700 x 3600 NB 2700 x 3600 | NT 3200 x 4500 NB 3200 x 4500 | NT 3600 x 5500 NB 3600 x 5500 | ||
1 đường kính trong của thùng | 900 | 1200 | 1500 | 2100 | 2700 | 3200 | 3600 | |
2 Chiều dài thùng, mm | 1800 | 2400 | 3000 | 3000 | 3600 | 4500 | 5500 | |
3 Dung tích danh nghĩa của thùng m3 | 0,9 | 2,0 | 4,0 | 8,5 | 17,5 | 32 | 49 | |
4 Kích thước choán chỗ, của máy, không lớn hơn, mm | Dài L | 3800 | 4500 | 630 | 9100 | 10.000 | 14.100 | 14.500 |
Rộng E | 2200 | 2500 | 3600 | 5900 | 6.400 | 7.430 | 7.600 | |
Cao H | 1600 | 2100 | 2600 | 3900 | 5.100 | 5620 | 5700 | |
5 Tần số quay danh nghĩa của thùng, tính bằng % của tần số quay tới hạn | NT | 60 ÷ 72 | ||||||
NB | 60 ÷ 86 | |||||||
6 Công suất động cơ điện, không lớn hơn, kw | 22 | 55 | 110 | 200 | 400 | 630 | 1,250 | |
7 Khối lượng toàn bộ, (không kể bì), không lớn hơn. tấn | 5,2 | 14 | 23 | 50 | 61 | 140 | 170 | |
8 Tổng khối lượng của vật nghiền, không lớn hơn, tấn | Thanh | 2,3 | 5,2 | 10,5 | 22,0 | 45,0 | 83,0 | 127,0 |
Bì | 1,7 | 3,8 | 7,7 | 16,5 | 34 | 61 | 94 |
CHÚ THÍCH
1. Dung tích danh nghĩa của thùng là dung tích được xác định sau khi lắp các tấm lót mới. Xem phụ lục của tiêu chuẩn.
2. Tần số quay của thùng được xác định theo tần số quay tới hạn do cơ quan thiết kế tính toán và được lựa chọn phù hợp với từng loại quặng cụ thể. Xem phụ lục của tiêu chuẩn.
Ví dụ ký hiệu của quy ước của máy nghiền bi, cấp và tháo liệu trung tâm đường kính thùng nghiền 1500 mm, chiều dài 1600 mm.
Máy nghiền NB 1500 x 1600 TCVN 4302 : 1986.
2.1. Tất cả các máy nghiền phải được chế tạo theo bản thiết kế được duyệt phù hợp với tiêu chuẩn và đạt được mọi yêu cầu kỹ thuật quy định trong tiêu chuẩn này.
2.2. Bộ truyền động của máy được đặt ở phía tháo liệu bên phải hoặc bên trái thùng.
2.3. Các chi tiết của bộ truyền động, của các ổ đỡ, của thân máy; các chi tiết của lớp lót và các chi tiết thay thế trong cùng một kiểu, cỡ khi thiết kế và chế tạo phải đảm bảo tính lắp lẫn. Các mối ghép bích phải kín, không để nước quặng chảy ra ngoài khi máy làm việc.
Các chi tiết đã được tiêu chuẩn hóa phải được thực hiện theo các tiêu chuẩn đã ban hành.
2.4. Kết cấu của máy nghiền cần đảm bảo.
a) Khả năng cơ giới hóa việc thay thế lớp lót tại chỗ hoặc trên giá sửa chữa.
b) Khả năng tháo lắp các chi tiết thay thế, tháo xiết các bu lông bắt giữ của các mối ghép bu lông đai ốc.
c) Khả năng bôi trơn các ổ đỡ một cách đầy đủ và ổn định, đồng thời có điều kiện kiểm tra thường xuyên chế độ bôi trơn ở các ổ đó.
Đối với các máy nghiền có các đường kính thùng nghiền lớn hơn hoặc bằng 2100 mm phải có hệ thống bôi trơn tự động các ổ và các bánh răng truyền động.
Các bộ phận có bôi trơn phải có kết cấu kín, không để dầu, mỡ chảy ra ngoài.
2.5. Các chi tiết của lớp lót bên trong thùng nghiền phải được chế tạo bằng thép 110 M n 13D (110 é13P), có hình dạng và kích thước hợp lý để nâng cao tuổi thọ của chi tiết nâng cao hiệu quả nghiền và dễ dàng tháo lắp thay thế, đồng thời cần có số lượng bu lông bắt giữ qua thân thùng ít nhất để hạn chế dò rỉ nước quặng ra ngoài.
Cho phép sử dụng các loại vật liệu phi kim loại để chế tạo chi tiết của lớp lót nếu vật liệu đó đáp ứng được các điều kiện công nghệ của quá trình nghiền, chịu mài mòn, không kém thép 110 Mn13D có khả năng gia công chế tạo và có hiệu quả kinh tế.
CHÚ THÍCH - Tạm thời sử dụng các tiêu chuẩn Liên Xô hay các tiêu chuẩn tương ứng của nước khác cho đến khi ban hành tiêu chuẩn Việt Nam về vật liệu.
2.6. Không được phép để nước quặng chảy hoàn toàn giữa lớp lót và mặt trong vỏ thùng.
2.7. Hình dạng bên ngoài của máy nghiền cần phải phù hợp với các yêu cầu kỹ thuật công nghiệp. Kết cấu của máy phải đảm bảo các yêu cầu an toàn cho người vận hành và môi trường xung quanh.
2.8. Mức độ gây tiếng ầm của máy nghiền khi làm việc ở cả trong định mức không vượt quá trị số cho phép trong TCVN 3985 : 1985.
2.9. Các bề mặt không chịu ma sát hoặc không lắp ghép với các chi tiết khác cần phải được sơn phủ thích hợp.
2.10. Các máy nghiền phải được xuất xưởng một cách đồng bộ và hoàn chỉnh, sản phẩm cần có đủ:
a) Bộ thân máy nghiền với lớp lót, vật nghiền, các gối đỡ thân máy, bộ truyền động, bộ phận cấp liệu, động cơ điện, bu lông móng, hệ thống bôi trơn, và các chi tiết phụ khác;
b) Các bộ phận và chi tiết dự phòng: trục truyền động, bánh răng nhỏ cùng các ổ lăn, bộ phận cấp liệu, đệm kín cho các gối đỡ thân máy, các chi tiết của lớp lót, (kể cả ống lót bên trong hai cổ trục của thùng) các bu lông phi tiêu chuẩn, các vòng đệm kín, một bộ bạc lót gối đỡ thân máy, một bộ tấm lưới cửa tháo liệu cùng với các nêm chèn, theo bản vẽ và hướng dẫn sử dụng đã quy định;
c) Các dụng cụ tháo lắp đặc biệt sử dụng cho việc tháo lắp, sửa chữa máy.
2.11. Thời gian bảo hành máy là 12 tháng kể từ khi giao máy cho khách hàng, với điều kiện người sử dụng phải tuân theo đúng quy tắc vận hành và bảo quản ghi trong bản hướng dẫn về lắp ráp, vận hành và bảo quản do cơ sở chế tạo lập.
2.12. Thời gian sử dụng một số chi tiết sau đây của máy nghiền không ít hơn:
- Lớp lót : 7000 giờ;
- Bánh răng dẫn (bánh nhỏ) : 7000 giờ;
- Các bạc lót ổ trượt gối đỡ thân máy : 7000 giờ.
3.1. Mỗi máy nghiền đều phải tiến hành lắp ráp kiểm tra tại cơ sở chế tạo theo chỉ dẫn của bản hướng dẫn về lắp ráp, vận hành và bảo quản.
3.2. Việc kiểm nghiệm các máy nghiền theo các điều quy định của tiêu chuẩn này phải tiến hành trong điều kiện vận hành với tải trọng định mức và kéo dài trong 72 giờ, trong thời gian đó có những lần dừng máy không quá 30 phút, để kiểm tra xem xét.
Kết quả kiểm nghiệm phải được lập thành văn bản.
3.3. Sau mỗi lần cải tiến kết cấu máy cơ sở chế tạo phải tiến hành thử nghiệm mẫu mới để kiểm tra xem sự phù hợp của các chỉ tiêu kỹ thuật của máy theo các yêu cầu của tiêu chuẩn này.
4. Ghi nhãn, bao gói, vận chuyển, bảo quản
4.1. Ở vị trí dễ thấy của máy phải gắn nhãn máy bằng tấm kim loại không bị rỉ, trên nhãn máy có các nội dung sau:
a) Nhãn hiệu hàng hóa của cơ sở chế tạo;
b) Tên gọi, ký hiệu và quy cách máy;
c) Số thứ tự sản xuất theo quy định của nhà máy;
d) Số hiệu tiêu chuẩn này;
e) Năm, tháng sản xuất;
f) Khối lượng máy;
g) Dấu chất lượng sản phẩm của nhà nước (nếu có).
4.2. Những chi tiết quan trọng của máy, ở vị trí được chỉ dẫn trên bản vẽ phải có nhãn hiệu và số hiệu quy định riêng của nhà máy chế tạo.
4.3. Các bề mặt lắp ghép của chi tiết khi tháo ra phải phủ một lớp mỡ chống rỉ tốt trong thời hạn ít nhất là một năm, các lỗ nhỏ cần được bịt kín.
4.4. Máy phải được chuyên chở đến nơi lắp đặt dưới dạng các bộ phận lắp sẵn hoặc các chi tiết tháo rời để dễ vận chuyển, những bộ phận và chi tiết nhỏ, thiết bị điện, các tài liệu kỹ thuật kèm theo máy phải đóng trong các hòm chắc chắn, vách trong của các hòm phải có lớp giấy dầu hoặc nilông chống nước.
4.5. Trên các hòm phải in dấu, và ghi rõ: “chống ẩm”, “không dễ lật”, “dây cẩu móc vào đây”…
4.6. Các bộ phận và chi tiết của máy khi bao gói, đóng kiện, và vận chuyển cần phải kê chèn đệm, lót cẩn thận để không gây hư hại khi chuyên chở và bốc dỡ;
4.7. Mỗi máy nghiền khi xuất xưởng phải kèm theo các tài liệu sau:
a) Lý lịch máy;
b) Bản hướng dẫn về lắp ráp vận hành và bảo quản máy;
c) Các bản vẽ gồm:
- Sơ đồ và các số liệu cần thiết cho việc thiết kế và làm móng máy;
- Bản vẽ chung;
- Bản vẽ các bộ phận và các chi tiết mau mòn, mau hỏng;
- Sơ đồ hệ thống bôi trơn và cấp điện.
d) Những bản liệt kê ghi rõ tên gọi, số lượng các bộ phận và chi tiết, kể cả phần dự phòng;
e) danh mục các dụng cụ dùng để tháo lắp.
4.9. Trong khi chờ đợi lắp đặt lên bệ móng, máy phải được cất giữ trong kho theo quy định về bảo quản cất giữ đã hướng dẫn.
Lựa chọn chiều dày lớp lót, tính khối lượng vật nghiền, tính tần số quay tới hạn, tính năng suất máy nghiền.
1. Chiều dày lớp lót (để thiết kế chế tạo và xác định dung tích danh nghĩa của thùng) được chọn theo đường kính trong của thùng theo Bảng sau:
Đường kính trong của thùng | Chiều dày lớp lót |
500 | 50 |
900 | 70 |
1200, 1500, 2100 | 100 |
2700, 3200, 3600 | 120 |
2. Khối lượng vật nghiền tính theo công thức:
trong đó:
G là khối lượng vật nghiền, t;
j là hệ số điện đẩy của vật nghiền đối với vật nghiền là bi cầu bằng 15 ± 50 %; đối với vật nghiền là thanh trụ bằng 35 ± 40 %;
V là dung tích danh nghĩa của thùng m3;
g là khối lượng đống trung bình của 1 m3 vật nghiền, t/m3.
- là đối với vật nghiền là bi cầu bằng 4,6;
- là đối với vật nghiền là thanh trụ bằng 6,6.
3. Tần số quay tới hạn của thùng nghiền được xác định theo công thức:
trong đó:
nth là tần số quay tới hạn của thùng nghiền vg/ ph;
Di là đường kính trong của thùng nghiền sau khi đã có lớp lót, m.
4. Năng suất cấp liệu xác định theo sản phẩm rắn thu được không nhỏ hơn 6 m3/ h trên 1 m³ dung tích danh nghĩa của thùng.
5. Năng suất máy nghiền theo quặng dầu cho từng trường hợp cụ thể tính theo công thức:
trong đó:
q là năng suất riêng của máy theo cấp hạt tính toán mới tạo thành; t/ m³. h;
V là dung tích làm việc danh nghĩa của thùng nghiền, m³;
b2 là hàm lượng cấp hạt tính toán trong sản phẩm, xác định theo phần đơn vị.
b1 là hàm lượng cấp hạt tính toán trong liệu cấp vào máy, xác định theo phần đơn vị.