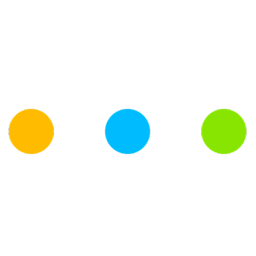
- 1 Decision No. 66/2008/QD-BLDTBXH of December 29, 2008, promulgating the process of safe technical testing for elevators, lifts and escalator
- 2 Decision No. 67/2008/QD-BLDTBXH of December 29, 2008, promulgating the process of safe technical testing for boilers, pressure vessels, refrigeration system, gas charge, processing system, gas cylinders and pipelines of steam, hot water
- 1 Decree No. 45/2013/ND-CP of May 10, 2013,elaborating a number of articles of the labor code on hours of work, hours of rest, occupational safety and occupational hygiene
- 2 Decree No. 106/2012/ND-CP of December 20, 2012, defining the functions, tasks, powers and organizational structure of the ministry of labor, war invalids and social affairs
MINISTRY OF LABOR – INVALIDS AND SOCIAL AFFAIRS | SOCIALIST REPUBLIC OF VIETNAM |
No. 07/2014/TT-BLDTBXH | Hanoi, 06 March 2014 |
Pursuant to the Government’s Decree No. 106/2012/ND-CP dated 20 December 2012 on the functions, missions, authority and organizational structure of the Ministry of Labor - Invalids and Social affairs;
Pursuant to the Government’s Decree No. 45/2013/ND-CP on the details of certain articles of the Labor Code, which stipulate work time, rest time, work safety and hygiene;
At the request of the Head of the Department of Work safety;
Minister of Labor - Invalids and Social affairs issues the Circular on 27 technical safety inspection procedures for machinery and equipment subject to strict work safety requirements under the management of the Ministry of Labor - Invalids and Social affairs.
Article 1. Scope of regulation
This Circular is enclosed with 27 technical safety inspection procedures for machinery and equipment subject to strict work safety requirements under the management of the Ministry of Labor - Invalids and Social affairs. Names and codes of the procedures are defined in Appendices of this Circular.
1. This Circular comes into force as of 01 May 2014.
2. Decision No. 66/2008/QD-BLDTBXH dated 29 December 2008 on technical safety inspection procedures for lifting equipment, elevator and escalator; Decision No. 67/2008/QD-BLDTBXH dated 29 December 2008 on technical safety inspection procedures for boiler, pressure vessel, refrigerant system, gas preparation and loading system, gas cylinder, steam pipe and hot water pipe; Circular No. 01/2010/TT-BLDTBXH dated 12 January 2010 on technical safety inspection procedures for passenger cableway, roller coaster and slides shall lose effect when this Circular comes into force.
Department of Work safety, Ministry of Labor - Invalids and Social affairs, technical work safety inspection organizations and entities concerned are responsible for enforcing this Circular. Difficulties that arise during the implementation of this Circular shall be reported to the Ministry of Labor - Invalids and Social affairs for consideration and settlement./.
| PP MINISTER |
Inspection procedure 1
FIELD DATA ACQUISITION FORM (TECHNICAL SAFETY INSPECTION FOR OVERHEAD LIFTING EQUIPMENT)
......, …, date: ... ... ...
FIELD DATA ACQUISITION FORM
(Record of full parameters for inspection and test as per the inspection procedure)
1. General information
Name of the equipment:
Name of the requester:
Address (head office):
Address (location) of equipment installation:
Details of the work session:
- Participants: (details)
- Witness:
2. Basic parameters of the equipment:
- Code: ………… | - Trolley speed: … meter/ minute |
- Production number: … | - Bridge speed : … meter/ minute |
- Year of production: … | - Aperture, cantilever: ... m |
- Manufacturer: ... | - Height of lift (main and auxiliary hooks): … m |
- Intended load capacity: … ton | - Load capacity at cantilever’s end : … ton |
- Lifting speed: … meter/ minute | - Function: … |
3. Inspection of documents:
- Profile of the equipment:
- Technical documents:
4. Measurement device identification code:
5. Equipment inspection:
a) External inspection:
+ Metal structure
+ Hook block, sheave: …
+ Rope and rope fixation: …
+ Protective ground connection:
+ Rail, rail fixation:
+ Brake: ...
+ Safety instruments:
b) Technical inspection:
- 125% overload test (10-minute hold):
+ Brake: ...
+ Metal structure: …
- 110% dynamic load test:
+ Brake (load holding)
+ Constituents or parts:
+ Metal structure:
6. Inspection of limiters, load indicator, overload indicator.
7. Processing of findings of the inspection.
8. Recommendation: (if any)
| INSPECTOR |
RECORD OF TECHNICAL SAFETY INSPECTION FOR OVERHEAD LIFTING EQUIPMENT
(Superior organization) | SOCIALIST REPUBLIC OF VIETNAM |
| .........… date: ... ... ... |
RECORD OF TECHNICAL SAFETY INSPECTION
(FOR OVERHEAD LIFTING EQUIPMENT)
No. …
The participants include:
1………Inspector’s number: ………
1………Inspector’s number: ………
Inspection organization: ………
Inspection organization’s registered certificate number: ………
Name of the equipment inspected: ………
Name of the requester:
Address (head office):
Address (location) of equipment installation:
Inspection procedure and standards applied: ………
Individuals witnessing and ratifying the record: ………
1...................................................... Position: ………
2...................................................... Position: ………
I. BASIC PARAMETERS OF THE EQUIPMENT
- Code: ………… - Trolley speed: … meter/ minute
- Production number: … - Bridge speed: … meter/ minute
- Year of production: … - Aperture, cantilever: ... m
- Manufacturer: ... - Height of lift (main and auxiliary hooks): … m
- Intended load capacity: … ton - Load capacity at cantilever's end: … ton
- Lifting speed: ... meter/ minute - Function: ...
II. FORM OF INSPECTION
First time □ Periodic □ Random □
III. DETAILS OF INSPECTION:
A. Inspection of technical documents:
- Remark: ………
- Assessment of findings:
No. | Item | Pass | Fail | Note |
1 | Profile |
|
|
|
B. External inspection and no-load test
- Remark: ………
- Assessment of findings:
No. | Constituent | Pass | Fail | Note |
1 | Main and auxiliary hooks |
|
|
|
2 | Pulley block |
|
|
|
3 | Main lift rope |
|
|
|
4 | Auxiliary lift rope |
|
|
|
5 | Main lift brake |
|
|
|
6 | Auxiliary lift brake |
|
|
|
7 | Trolley brake |
|
|
|
8 | Rail, rail gauge |
|
|
|
9 | Metal structure of main girders; attachments to the building |
|
|
|
10 | Hoist motor frame |
|
|
|
11 | Hoist motor brake |
|
|
|
12 | Main lifting mechanism |
|
|
|
13 | Auxiliary lifting mechanism |
|
|
|
14 | Trolley motion mechanism |
|
|
|
15 | Hoist motor motion mechanism |
|
|
|
16 | Rail clip |
|
|
|
17 | Siren (buzzer) |
|
|
|
18 | Height limit switch |
|
|
|
19 | Trolley motion controller |
|
|
|
20 | Electrical system |
|
|
|
21 | Control system |
|
|
|
22 | Hoist motor motion controller |
|
|
|
C. Load test
- Remark: ………
- Assessment of findings:
No. | Load positions and findings | Pass | Fail | Equivalent load (ton) | Static load test (ton) | Dynamic load test (ton) |
1 | Mid-aperture |
|
|
|
|
|
2 | At cantilever’s end |
|
|
|
|
|
3 | Stability |
|
|
|
|
|
No. | Assessment of findings | Pass | Fail | Note |
1 | Metal structure: |
|
|
|
2 | Control system |
|
|
|
3 | Overload prevention device |
|
|
|
4 | Lifting rope |
|
|
|
5 | Lift brake |
|
|
|
6 | Trolley brake |
|
|
|
7 | Hoist motor brake |
|
|
|
IV. CONCLUSION AND RECOMMENDATION
1. The equipment inspected is: Qualified □ Unqualified □
to operate with the maximum load of … ton
2. Inspection stamp no … Stamp position: ...
3. Recommendation:
Time limit for implementation of recommendations: …
V. INSPECTION SCHEDULE
The following inspection shall be scheduled for ... [date]
Reason for early inspection schedule (if applicable): …
The record was ratified on … [date]
At: …
The record is made into ... originals. Each party keep ... original(s)
The inspectors assume all liabilities for the accuracy of remark and assessments in this record./.
EQUIPMENT USER | WITNESS | INSPECTOR |
Inspection procedure 3
FIELD DATA ACQUISITION FORM (TECHNICAL SAFETY INSPECTION FOR ELECTRIC ELEVATOR)
......, …, date: ... ... ...
FIELD DATA ACQUISITION FORM
(Record of full parameters for inspection and test as per the inspection procedure)
1. General information
Name of the equipment:
Name of the requester:
Address (head office):
Address (location) of equipment installation:
Details of the work session:
- Participants: (details)
- Witness:
2. Basic parameters of the equipment:
Code: | Year of production: | Rated speed: |
Quantity of stops: | Production number: | Rated load: |
Manufacturer:
3. Inspection of documents:
- Profile of the equipment:
- Technical documents:
4. Measurement device identification code:
5. a) External inspection:
- Insulation resistance:
- Machine room:
- Motor parameters:
Capacity | Year of production: | Rated current: |
Code: | Serial number: | Voltage: |
Manufacturer: | Rotary speed: |
|
- Inspection of hoist rope and counterweight:
- Inspection of roller guides:
6. Dimensions and distance (mm):
- Elevator pit:
- Distance from the pit’s bottom to buffer’s tip upon full compression:
- Distance from counterweight’s bottom to the buffer’s tip upon full compression:
- Distance from the pit’s bottom to the car’s lowest position:
- Distance from the car's roof to the head room's lowest position:
- Distance from the entrance door’s threshold to the car’s doorstep:
- Distance from the counterweight to the car:
7. Technical inspection:
- Empty load test:
- 100% load test; + Motor’s electric current:
+ Speed:
+ Maximum floor arrival precision deviation:
- 125% load test: + Electromagnetic brake:
+ Safety gear:
+ Push pull test:
- + Automatic rescue device test:
- Overload prevention device:
- Test of elevator operation upon fire or earthquake (if applicable):
8. Recommendation: (if any)
| INSPECTOR |
RECORD OF TECHNICAL SAFETY INSPECTION FOR ELECTRIC ELEVATOR
(Superior organization) | SOCIALIST REPUBLIC OF VIETNAM |
| ............ ... ..., date ... ... ... ... |
RECORD OF TECHNICAL SAFETY INSPECTION
(FOR ELECTRIC ELEVATOR)
No. …
The participants include:
1………Inspector’s number: ………
1………Inspector’s number: ………
Inspection organization: ………
Inspection organization’s registered certificate number: ………
Name of the equipment inspected: ………
Name of the requester:
Address (head office):
Address (location) of equipment installation:
Inspection procedure and standards applied: ………
Individuals witnessing and ratifying the record: ………
1................................................... Position: ………
2................................................... Position: ………
I. PARAMETERS OF THE ELEVATOR
Elevator type: | Year of production: | Rated speed (meter/ minute): |
Code: | Production number: | Rated load (Kg): |
Manufacturer: | Quantity of stops: | Purpose of use: |
II. FORM OF INSPECTION
First time □ Periodic □ Random □
III. DETAILS OF INSPECTION:
1. DOCUMENT INSPECTION:
- Remark: ………
- Assessment of findings:
No. | ITEM | PASS | FAIL | NOTE |
1 2 | Profile Technical documents: |
|
|
|
2. EXTERNAL INSPECTION:
- Remark: ………
Elevator completeness and synchronization: …
Defects and deformation: …
- Assessment of findings: Pass □ Fail □
3. TECHNICAL INSPECTION AND EMPTY LOAD TEST:
- Remark: ………
- Assessment of findings:
No. | ITEM | PASS | FAIL | NOTE |
1 | Elevator pit |
|
|
|
2 | Machine room |
|
|
|
3 | Motor |
|
|
|
4 | Gearbox |
|
|
|
5 | Electromagnetic brake |
|
|
|
6 | Roller guide |
|
|
|
7 | Overspeed governor |
|
|
|
8 | Suspension rope |
|
|
|
9 | Sheaves |
|
|
|
10 | Car |
|
|
|
11 | Counterweight |
|
|
|
12 | Buffer |
|
|
|
13 | Safety gear |
|
|
|
14 | Electrical system |
|
|
|
15 | Final terminal limit protection |
|
|
|
16 | Entrance door - door control |
|
|
|
17 | Distance from the pit’s bottom to car's lowest position: |
|
|
|
18 | Distance from the car’s roof to the head room’s lowest position |
|
|
|
19 | Distance from the entrance door’s threshold to car’s doorstep: |
|
|
|
4. DYNAMIC TEST OF 100% RATED LOAD:
- Remark: ………
- Assessment of findings: |
|
|
|
|
|
+ Car speed: | Result: | Pass | □ | Fail | □ |
+ Electric current in the motor: | Result: | Pass | □ | Fail | □ |
+ Maximum floor arrival precision deviation: | Result: | Pass | □ | Fail | □ |
+ Instantaneous safety gear with or without buffered effect:
Result: Pass □ Fail □
5. DYNAMIC TEST OF 125% RATED LOAD:
- Remark: ………
- Assessment of findings: |
|
|
|
|
|
+ Electromagnetic brake | Result: | Pass | □ | Fail | □ |
+ Progressive safety gear | Result: | Pass | □ | Fail | □ |
+ Push pull test: | Result: | Pass | □ | Fail | □ |
6. RESCUE SYSTEM TEST: |
|
|
|
|
|
- Remark: ………
- Assessment of findings:
+ Automatic rescue device (if available) Result: Pass □ Fail □
+ Communications system (bell, emergency phone)
Result: Pass □ Fail □
IV. CONCLUSION AND RECOMMENDATION
1. The elevator inspected is: Qualified □ Unqualified □
to operate with the maximum load of … (kg)2. Inspection stamp no … appended at …
3. Other recommendations (if any): …
Time limit for implementation of recommendations: …
V. INSPECTION SCHEDULE
The following inspection shall be scheduled for ... [date]
Reason for early inspection schedule (if applicable): …
The record was ratified on … [date]
At: …
The record is made into ... originals. Each party keep ... original(s)
The inspectors conducting the inspection of the elevator assume all liabilities for the accuracy of remarks and assessments in this record./.
EQUIPMENT USER | WITNESS | INSPECTOR |
Inspection procedure 08
FIELD DATA ACQUISITION FORM (TECHNICAL SAFETY INSPECTION FOR INDUSTRIAL GAS CYLINDERS)
......, …, date: ... ... ...
FIELD DATA ACQUISITION FORM
(Record of full parameters for inspection and test as per the inspection procedure)
Inspection schedule: First time □; Periodic □; Random □
User
Production number, batch number: (1)
Month and year of production: (2)
Type of cylinder (by volume): Hydraulic test pressure (Bar):
Tightness test pressure (Bar):
Inspector | Signature | Performer of visual inspection | Signature |
Performer of hydraulic test | Signature | Performer of tightness test | Signature |
Weight (kg) Result of inspection
| Code | Production number | Month and year of production | Manufacturer | Weight (kg) | Result of inspection | |||
On label | Actual | Pass | Early inspection schedule (specify reasons) | Fail (specify reasons) | |||||
1 |
|
|
|
|
|
|
| (3) |
|
2 |
|
|
|
|
|
|
|
| (4) |
3 |
|
|
|
|
|
|
|
|
|
4 |
|
|
|
|
|
|
|
|
|
5 |
|
|
|
|
|
|
|
|
|
· (1), (2) for cylinders inspected for the first time.
· (3) for example: 02 years due to cylinders’ containment of gases corroding metal or posing hazards
· (4) for example: cylinders failed due to damaged cylinder neck thread
| INSPECTOR |
RECORD OF TECHNICAL SAFETY INSPECTION FOR INDUSTRIAL GAS CYLINDERS
(Superior organization) | SOCIALIST REPUBLIC OF VIETNAM |
| ................. ... ..., date ... ... ... ... |
RECORD OF TECHNICAL SAFETY INSPECTION
(FOR INDUSTRIAL GAS CYLINDERS)
The participants include:
1………Inspector’s number: ………
2………Inspector’s number: ………
Inspection organization: …
Inspection organization’s registered certificate number: ………
Having inspected: …
Under ownership of (name of the organization):
Address (head office): …
Location of inspection: …
Inspection procedures applied: ………
Individuals witnessing and ratifying the record: ………
1.......................................................... Position:................................................
2.......................................................... Position:................................................
I. BASIC PARAMETERS OF CYLINDERS
Name and address of the manufacturer: …
Month and year of production: …
Batch number: …
Quantity and list of sample cylinders inspected: …
The brand name embossed on cylinders: …
Intended pressure:........................... bar Test pressure:.........................................bar
Volume: … liters Tare weight: … kg
Function: …
Previous date of inspection: … By: …
II. FORM OF INSPECTION
First time □; Periodic □; Random □
III. DETAILS OF INSPECTION:
1. Inspection of documents and profile:
Item | Pass | Fail | Item | Pass | Fail |
Cylinder batch list |
|
| Result of cylinder batch inspection |
|
|
Result of strength and tightness tests: |
|
| Result of volumetric expansion test |
|
|
Result of tests on materials’ mechanical properties and welds |
|
| Record of explosion test |
|
|
Result of thickness test |
|
| Result of ultrasonic test of welds |
|
|
Result of analysis of materials’ mechanical and chemical properties |
|
| Cylinder batch’s profile |
|
|
Documents on usage, inspection and other details of the cylinders |
|
| Other papers |
|
|
Assessment of findings:
- Remark: ………
- Result: Pass □ Fail □
2. External and internal inspection:
Item | Pass | Fail: | Item | Pass | Fail |
Conditions of cylinder shroud |
|
| Conditions of external metal surface |
|
|
Conditions of cylinder foot |
|
| Conditions of internal metal surface |
|
|
Cylinder valve: |
|
| Weld surface conditions |
|
|
- Remark: ………
- Result: Pass □ Fail □
3. Test:
Entry | Reagent | Test pressure (bar): | Duration (minute) |
Strength test |
|
|
|
Volumetric expansion test |
|
|
|
Tightness test |
|
|
|
- Remark: ………
- Result: Pass □ Fail □
IV. CONCLUSION AND RECOMMENDATION
1. The batch (specify the quantity of cylinders) inspected is: Qualified □ Unqualified □
2. Inspection mark has been appended on: …
3. Operational pressure: … bar
4. Recommendation:
5. Time limit for implementation of recommendations: …
V. INSPECTION SCHEDULE
Periodic inspection shall be scheduled for ... [date]
The record was made on … [date]
At: (Specify the location of inspection)
The inspectors conducting the inspection assume all liabilities for the accuracy of remarks and assessments in this record./.
1. For the inspection done at the inspection organization’s station:
HEAD OF THE STATION | INSPECTOR | TECHNICIAN |
2. For the inspection done at the concerned organization’s premises:
HEAD OF THE ORGANIZATION | WITNESS | INSPECTOR |
LIST OF SAMPLE CYLINDERS INSPECTED
Cylinder batch:
Quantity of cylinders:
Production number: from … to…
User (manager):
(Enclosed with the record or certificate of registration no …dated …),
No. | Production number | Month and year of production | Manufacturer | Weight (kg) | Result: | |
Pass | Fail (specify reasons) | |||||
1 |
|
|
|
|
|
|
2 |
|
|
|
|
|
|
... |
|
|
|
|
|
|
LIST OF CYLINDERS EXCLUDED (OR LIST OF CYLINDER BATCHES)
Cylinder batch:
Quantity of cylinders excluded:
User (manager):
No. | Production number | No. | Production number | No. | Production number | No. | Production number |
1 |
|
|
|
|
|
|
|
2 |
|
|
|
|
|
|
|
... |
|
|
|
|
|
|
|
Note:
+ Draw up the “LIST OF CYLINDERS EXCLUDED” for the cylinder batch with continuous production numbers or with few cylinders excluded (for the manufacturer’s test of mechanical properties, destructive test, etc.) or draw up the “LIST OF CYLINDER BATCHES” and specify the full amount of cylinders in the batch for the cylinder batch with interrupted production numbers. + This list may not be required if there are only a few cylinders to be directly enumerated in the record.
Notice: This list must not be modified. The list must be stamped on its corner or fan stamped.
LIST OF CYLINDER BATCHES INSPECTED
Cylinder batch:
Quantity of cylinders:
Production number: from … to …
User (manager):
(Enclosed with the record or certificate of registration no … dated …)
No. | Production number | Month and year of production | Manufacturer | Weight (kg) | Result: | |
Pass | Fail (specify reasons) | |||||
1 |
|
|
|
|
|
|
2 |
|
|
|
|
|
|
... |
|
|
|
|
|
|
Inspection procedure 19
FIELD DATA ACQUISITION FORM (FOR MOBILE CRANE)
......, …, date: ... ... ...
FIELD DATA ACQUISITION FORM
(Record of full parameters for inspection and test as per the inspection procedure)
1. General information
Name of the equipment:
Name of the requester: …
Address (head office): …
Address (location) of equipment installation:
Details of the work session:
- Participants: (details)
- Witness:
2. Basic parameters of the equipment:
- Code: … | - Rotary speed: … rotation/ minute |
- Production number: … | - Travelling speed (for self-propelled ones): … meter/ minute |
- Year of production: … | - Working radius (max): … meter |
- Manufacturer: … | - Lifting height (main and auxiliary hooks): … meter |
- Intended load (max): … ton | - Load at maximum radius: … ton |
- Lifting speed: … m/ minute | - Function: … |
3. Inspection of documents:
- Profile of the equipment:
- Technical documents:
4. Measurement device identification code:
5. Inspection of the equipment:
a) External inspection:
- Metal structure:
- Load block, sheave: …
- + Rope and rope fixation: …
- Hydraulic system, piston, cylinder:
- Brake:
- Counterweight: …
- Safety devices:
b) Technical inspection:
- Test at 125% rated load (10-minute hold):
- Brake:
- + Metal structure:
- Dynamic test at 110% rated load:
- + Brake (load holding)
- Constituents or parts:
- Metal structure:
6. Inspection of limiters, load indicator, overload indicator.
7. Processing and assessment of findings of the inspection.
8. Recommendation: (if any)
| INSPECTOR |
RECORD OF TECHNICAL SAFETY INSPECTION
(FOR MOBILE CRANE)
(Superior organization) | SOCIALIST REPUBLIC OF VIETNAM |
| ................. ... ..., date ... ... ... ... |
RECORD OF TECHNICAL SAFETY INSPECTION
(FOR MOBILE CRANE)
No. …
The participants include:
1. Inspector’s number:
2. Inspector’s number:
Inspection organization: ………
Inspection organization’s registered certificate number: ………
Name of the equipment inspected: ………
Name of the requester:
Address (head office): …
Address (location) of equipment installation:
Inspection procedure and standards applied: ………
Individuals witnessing and ratifying the record: ………
1. ...................................... Position:..................................
2. ...................................... Position:..................................
I. BASIC PARAMETERS OF THE EQUIPMENT
- Code: … | - Rotary speed: … rotation/ minute |
- Production number: … | - Travelling speed (for self-propelled ones): … meters/ minute |
- Production number: … | - Actual / intended radius: … meter |
- Manufacturer: … | - Actual / intended lifting height (main and auxiliary hooks): … meter |
- Intended load (max): … ton | - Load at maximum actual / intended radius: … ton |
- Lifting speed: … meter/ minute | - Function: … |
II. FORM OF INSPECTION
First time □, periodic □, random □
III. DETAILS OF INSPECTION:
A. Document inspection:
No. | Entry | Pass | Fail | Note |
| No. | Entry | |
1 | Profile |
|
|
|
| 2 | Number plate | …………. |
B. External inspection and no-load test:
No. | Constituents and parts | Pass | Fail | Note |
1 | Main and auxiliary hooks |
|
|
|
2 | Pulley block |
|
|
|
3 | Main lifting rope |
|
|
|
4 | Auxiliary lifting rope |
|
|
|
5 | Boom bearing |
|
|
|
6 | Boom guy line |
|
|
|
7 | Main lifting part |
|
|
|
8 | Wind speed indicator |
|
|
|
9 | Height limiter |
|
|
|
10 | Boom angle limiter |
|
|
|
11 | Counterweight |
|
|
|
12 | Travel drive part |
|
|
|
13 | Main lift brake |
|
|
|
14 | Travel brake |
|
|
|
15 | Auxiliary lifting part |
|
|
|
16 | Boom lifting part |
|
|
|
17 | Boom extension part |
|
|
|
18 | Outrigger (chain) |
|
|
|
19 | Siren and buzzer |
|
|
|
20 | Metal structure and boom |
|
|
|
21 | Hoist motor frame |
|
|
|
22 | Auxiliary lift brake |
|
|
|
23 | Boom lift brake |
|
|
|
24 | Indicators of radius and equivalent load |
|
|
|
25 | Control system |
|
|
|
26 | Hydraulic system |
|
|
|
27 | Rotating part |
|
|
|
28 | Brake for rotating part |
|
|
|
C. Load test
No. | Load positions and findings | Pass | Fail | Radius (m) |
| Equivalent load (ton) | Static load test (ton) | Dynamic load test (ton) |
1 | Minimum radius |
|
| R = |
|
|
|
|
2 | Maximum radius |
|
| R = |
|
|
|
|
3 | Auxiliary hook |
|
|
|
|
|
|
|
4 | Main boom length |
|
|
|
|
|
|
|
5 | Stability |
|
|
|
|
|
|
|
No. | Assessment of findings | Pass | Fail | Note |
1 | Metal structure: |
|
|
|
2 | Load lift brake |
|
|
|
3 | Boom lift brake |
|
|
|
4 | Overload prevention device (if available) |
|
|
|
5 | Lift rope |
|
|
|
6 | Brake for rotating part |
|
|
|
7 | Travel brake |
|
|
|
8 | Outrigger (chain) |
|
|
|
9 | Hydraulic system |
|
|
|
10 | Control system |
|
|
|
IV. CONCLUSION AND RECOMMENDATION
1. The equipment inspected is: Qualified □ Unqualified □
2. Inspection stamp no … affixed at …
3. The equipment is functionally qualified for the maximum load of … ton at an equivalent radius of … meter
4. Recommendations:
Time limit for implementation of recommendations: …
V. INSPECTION SCHEDULE
Periodic inspection: …. [date]
Reason for early inspection schedule (if applicable): …
The record was ratified on … [date]
At: …
The record is made into ... originals. Each party keep ... original(s)
The inspectors conducting the inspection assume all liabilities for the accuracy of remarks and assessments in this record./.
HEAD OF THE CONCERNED PARTY | WITNESS | INSPECTOR |
Inspection procedure 21
FIELD DATA ACQUISITION FORM
(FOR FORKLIFT)
......, ... ... ..., date ... ... ... ...
FIELD DATA ACQUISITION FORM
(Record of full parameters for inspection and test as per the inspection procedure)
1. General information
Name of the equipment:
Name of the requester:
Address (head office): …
Address (location) of equipment installation:
Details of the work session:
- Participants: (details)
- Witness:
2. Basic parameters of the equipment:
- Code: ………… - Fork size: … mm
Production number: … - Lift height: … mm
- Year of production: … - Lift speed: … meter/ minute
- Manufacturer: ... - Travel speed: … kilometer/ hour
- Power source: … - Load center distance at maximum load: … mm
- Working / intended load: … / … kg - Function: …
3. Inspection of documents:
- Profile of the equipment:
- Technical documents:
4. Measurement device identification code:
5. Inspection of the equipment:
a) External inspection and no-load test:
- Fork: …
- Carriage: …
- Lift cylinder: …
- Tilt cylinder: …
- Load bearing cylinder: …
- Counterweight: …
- Overhead guard: …
- Signs that indicate radius and equivalent load: …
- System for signaling, observation, lighting: …
- Travel system: …
- Brake system: …
- Safety devices: …
b) Technical inspection:
- Test at 125% rated load (10-minute hold):
+ Brake: …
+ Metal structure: …
- Dynamic test at 110% rated load:
+ Brake (load holding)
+ Constituents and parts:
+ Metal structure:
7. Processing and assessment of findings of the inspection.
8. Recommendation: (if any)
| INSPECTOR |
RECORD OF TECHNICAL SAFETY INSPECTION
(FOR FORKLIFT)
(Superior organization) | SOCIALIST REPUBLIC OF VIETNAM |
| ..............…, date … … … |
RECORD OF TECHNICAL SAFETY INSPECTION
(FOR FORKLIFT)
No. …
The participants include:
1. Inspector’s number: …
2. Inspector’s number: …
Inspection organization: ………
Inspection organization’s registered certificate number: ………
Name of the equipment inspected: ………
Name of the requester:
Address (head office): …
Address (location) of equipment installation:
Inspection procedure and standards applied: ………
Individuals witnessing and ratifying the record: ………
1. ...................................... Position:..................................
2. ...................................... Position:..................................
I. BASIC PARAMETERS OF THE EQUIPMENT
- Type and code: … - Fork size: … mm
- Production number: … - Lift height: … mm
- Year of production: … - Lift speed: … meter/ minute
- Manufacturer: ... - Travel speed: … kilometer/ hour
- Power source: … - Load center distance at maximum load: … mm
- Working / intended load: … /… kg- Function: …
II. FORM OF INSPECTION
First time □, periodic □, random □
III. DETAILS OF INSPECTION:
A. Inspection of technical documents:
No. | Entry | Pass | Fail | Note |
1 | Profile of the equipment: |
|
|
|
2 |
|
|
|
|
B. External inspection and no-load test:
No. | Constituents and parts | Pass | Fail | Note |
1 | Load bearing |
|
|
|
2 | Carriage |
|
|
|
3 | Lift cylinder |
|
|
|
4 | Tilt cylinder |
|
|
|
5 | Load bearing cylinder |
|
|
|
6 | Counterweight |
|
|
|
7 | Overhead guard |
|
|
|
8 | Indicators of radius and equivalent load |
|
|
|
9 | Overload prevention device |
|
|
|
10 | Hydraulic system |
|
|
|
11 | Control system |
|
|
|
12 | System for signaling, observation, lighting: … |
|
|
|
13 | Motion-driving system |
|
|
|
14 | Travel system: … |
|
|
|
15 | Brake system |
|
|
|
16 | Lift height limiter |
|
|
|
17 | Tilting angle limiter |
|
|
|
C. Load test
No. | Load positions and findings | Pass | Fail |
| Static load test (ton) | Dynamic load test (ton) |
1 | On the fork |
|
|
|
|
|
2 | Stability |
|
|
|
No. | Assessment of findings | Pass | Fail | Note |
1 | Load bearing and carriage |
|
|
|
2 | System for signaling, observation and lighting |
|
|
|
3 | Overload prevention device |
|
|
|
4 | Travel system |
|
|
|
5 | Hydraulic system |
|
|
|
6 | Brake system |
|
|
|
7 | Motion-driving system |
|
|
|
IV. CONCLUSION AND RECOMMENDATION
1. The equipment inspected is: Qualified □ Unqualified □
to operate at the maximum load of … ton, with the equivalent load center distance of … mm
2. Inspection stamp no …was affixed at … of the forklift3. Recommendations:
Time limit for implementation of recommendations: …
V. INSPECTION SCHEDULE
The following inspection shall be scheduled for … [date]
Reason for early inspection schedule (if applicable): …
The record was ratified on … [date] at: …
The record is made into ... originals. Each party keep ... original(s)
The inspectors conducting the inspection assume all liabilities for the accuracy of remarks and assessments in this record./.
HEAD OF THE CONCERNED PARTY | WITNESS | INSPECTOR |
Inspection procedure 23
FIELD DATA ACQUISITION FORM
(FOR GOODS LIFT WITH ATTENDANTS)
......, …,date ... ... ...
FIELD DATA ACQUISITION FORM
(Record of full parameters for inspection and test as per the inspection procedure)
1. General information
Name of the equipment:
Name of the requester:
Address (head office): …
Address (location) of equipment installation:
Details of the work session:
- Participants: (details)
- Witness:
2. Basic parameters of the equipment:
- Type and code: | ................ | - Intended load: | .........… ton |
|
- Production number: | ................ | - Lift speed: | .........… meter / minute |
|
- Year of production: | ................ | - Lift height: | ........................ | meter |
- Manufacturer: | ................ | - Function: | .............................. |
|
3. Inspection of documents:
- Profile of the equipment:
- Technical documents:
- Inspection of design documents and foundation completion papers
- Data from the measurement of anti-lightning and ground wiring systems: …
4. Measurement device identification code:
5. Inspection of the equipment:
a) External inspection:
+ Inspection of the equipment’s location, electrical system, internal written guidelines on usage, protective fences, ground area, distance and safety measures.
+ Pillar platform structure:
+ Car buffer must be fully and firmly installed (according to design documents).
+ Barriers covering the equipment:
+ Entrance doors that the lift reaches:
+ Pillar body:
+ Car (cage):
+ Motion-driving part for the cage:
+ Fall protection unit:
+ Counterweight
+ Ground wiring unit:
+ Inspection of anti-lightning system:
+ Safety devices:
+ Brakes, electric motor, hydraulic drive system:
b) Technical inspection:
- Test at 125% rated load (10-minute hold):
+ Brake:
+ Metal structure: …
- Dynamic test at 110% rated load:
+ Brake (load holding)
+ Constituents and parts:
+ Metal structure:
c) Inspection of fall protection unit:
6. Inspection of limiters, load indicator, overload indicator.
7. Processing and assessment of findings of the inspection.
8. Recommendation (if any):
| INSPECTOR |
RECORD OF TECHNICAL SAFETY INSPECTION
(FOR GOODS LIFT WITH ATTENDANTS)
(Superior organization) | SOCIALIST REPUBLIC OF VIETNAM |
| ..............…, date … … … |
RECORD OF TECHNICAL SAFETY INSPECTION
(FOR GOODS LIFT WITH ATTENDANTS)
No. …
The participants include:
1. … Inspector’s number: ….
2. … Inspector’s number: ….
Inspection organization: ………
Inspection organization’s registered certificate number: ………
Name of the equipment inspected: ………
Name of the requester:
Address (head office): …
Address (location) of equipment installation:
Inspection procedure and standards applied: ………
Individuals witnessing and ratifying the record: ………
1. ...................................... Position:..................................
2. ...................................... Position:..................................
I. BASIC PARAMETERS OF THE EQUIPMENT
- Type and code: | .................... | - Intended load: | ..................... | ton |
- Production number: | .................... | - Lift speed: | ...................... | meter/minute |
- Year of production: | .................... | - Lift height: | ...................... | meter |
- Manufacturer: | .................... | - Function: | ........................... |
|
II. FORM OF INSPECTION
First time □, Periodic □, Random □
III. DETAILS OF INSPECTION:
A. Inspection of technical documents:
No. | Item | Pass | Fail | Note |
1 | Profile |
|
|
|
|
Ground foundation papers
|
|
|
|
B. External inspection and no-load test
No. | Constituents and parts | Pass | Fail | Note |
1 | Car |
|
|
|
2 | Gear box |
|
|
|
3 | Rack and pinion |
|
|
|
4 | Pillar’s metal structure |
|
|
|
5 | Anchored tie |
|
|
|
6 | Final terminal limit protection |
|
|
|
7 | Erection part |
|
|
|
8 | Load lifting part |
|
|
|
9 | Lift brake |
|
|
|
10 | Fall protection brake |
|
|
|
11 | Platform frame (buffer) |
|
|
|
12 | Siren and buzzer |
|
|
|
13 | Ground wiring |
|
|
|
14 | Anti-lightning |
|
|
|
15 | Safety barrier |
|
|
|
16 | Control system |
|
|
|
C. Load test (Upon inspection, the car lift height H = … meter)
Load positions and equivalent load test
No. | Load position | Pass | Fail | Equivalent load (ton) | Static load test (ton) | Dynamic load test (ton) |
1 | Inside the car |
|
|
|
|
|
2 | Stability |
|
|
|
No. | Load test result | Pass | Fail | Note |
1 | Pillar’s metal structure |
|
|
|
2 | Car structure |
|
|
|
3 | Lift brake |
|
|
|
4 | Gear box |
|
|
|
5 | Rack and pinion |
|
|
|
6 | Control system |
|
|
|
7 | Fall protection brake |
|
|
|
8 | Anchored tie |
|
|
|
9 | Overload indicator |
|
|
|
IV. CONCLUSION AND RECOMMENDATION
1. The equipment inspected is: Qualified □ Unqualified □ to operate at the maximum load of … kg.
2. Inspection stamp no …was affixed at … 3. Recommendations:
Time limit for implementation of recommendations: …
V. INSPECTION SCHEDULE
The following inspection shall be scheduled for … [date]
Reason for early inspection schedule (if applicable): …
The record was ratified on … [date]
At: …
The record is made into ... originals. Each party keep ... original(s)
The inspectors conducting the inspection assume all liabilities for the accuracy of remarks and assessments in this record./.
HEAD OF THE CONCERNED PARTY | WITNESS | INSPECTOR |
------------------------------------------------------------------------------------------------------
- 1 Decision No. 66/2008/QD-BLDTBXH of December 29, 2008, promulgating the process of safe technical testing for elevators, lifts and escalator
- 2 Decision No. 67/2008/QD-BLDTBXH of December 29, 2008, promulgating the process of safe technical testing for boilers, pressure vessels, refrigeration system, gas charge, processing system, gas cylinders and pipelines of steam, hot water
- 3 Circular No. 54/2016/TT-BLDTBXH dated December 28, 2016, 30 procedures for inspection of safety of machinery, equipment and supplies to which strict occupation safety requirements are applied under administration of Ministry of Labour, Invalids and Social Affairs
- 4 Circular No. 54/2016/TT-BLDTBXH dated December 28, 2016, 30 procedures for inspection of safety of machinery, equipment and supplies to which strict occupation safety requirements are applied under administration of Ministry of Labour, Invalids and Social Affairs
- 1 Circular No. 73/2014/TT-BTC dated May 30, 2014,
- 2 Circular No. 05/2014/TT-BLDTBXH dated March 6, 2014, promulgating list of machines, equipment and supplies having strict requirement on labor safety
- 3 Circular No. 06/2014/TT-BLDTBXH dated March 6, 2014, regulations on occupational safety inspection of machinery, equipment, supplies with strict requirements for occupational safety under the management of the ministry of labor, war invalids and social affairs
- 4 Decree No. 45/2013/ND-CP of May 10, 2013,elaborating a number of articles of the labor code on hours of work, hours of rest, occupational safety and occupational hygiene
- 5 Decree No. 106/2012/ND-CP of December 20, 2012, defining the functions, tasks, powers and organizational structure of the ministry of labor, war invalids and social affairs
- 1 Circular No. 73/2014/TT-BTC dated May 30, 2014,
- 2 Circular No. 05/2014/TT-BLDTBXH dated March 6, 2014, promulgating list of machines, equipment and supplies having strict requirement on labor safety
- 3 Circular No. 06/2014/TT-BLDTBXH dated March 6, 2014, regulations on occupational safety inspection of machinery, equipment, supplies with strict requirements for occupational safety under the management of the ministry of labor, war invalids and social affairs